Here are some of the signs on the main garage entrance to
the building. The sign on the bottom right says 'Scavenging is
Prohibited'. Most workers don't pay attention to that sign. We
see all kinds of stuff in the mixed recyclables that we sort. I now
have a hard hat (for future work) and won't say where I got it from.
Also, in our area the cold drink makers are running promotions with
'win a prize' under the caps of some soft drink bottles. Most soft drink
bottles don't have their caps, but many do and it has gotten so that my eyes
pick out bottles with promotional caps (most aren't, but the promotional
caps are non-standard colors for the brand). I set them aside when sorting
and check them when the line is stopped. One day I found 11 free 20 ounce
soft drink caps. That was a record! |
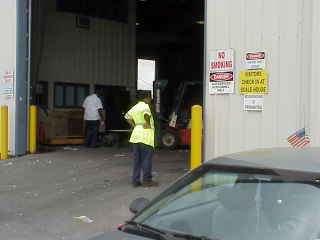 |
Here is Michael reading a book during a break in our break
area. He came to New Orleans from California with everything in his car (like
me), but has settled here for a few years at least. We won't say where the
books he reads come from, but I am sure that he recycles them appropriately
in any case (so it wouldn't be scavenging in any case as they are just a
little delayed in getting to their proper place). |
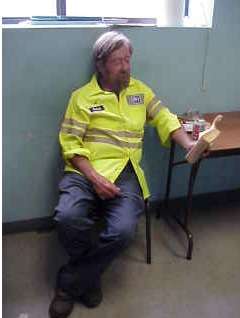 |
The line supervisor often checks the bins contents through
the day. I presume that she is checking for amount of work completed,
when to have the Bobcat make more room under the perforator, and for the
quality of the sorting. If there is a noticable amount of the wrong kind
of plastic, she will complain to the sorters. Of course it is difficult
to say where the improper materials come from as the Bobcat can mix
materials up from the back as can the two fail safe sorters (Dalton at end
of line and Billie on the return conveyor belt). However, we normally get
98 to 99% accuracy in our sorted material with the milk jugs usually
being best and mixed plastics being almost impossible to tell (as it is
all colors mixed together). It is rare for the line supervisor to make
such comments with the current crew (which is said to be a good crew). |
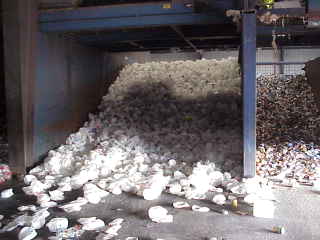 |
Here is the view of the break area and adminstrative area
from the end of the sorting line (left side of picture). Most of the
manager's offices are on the second floor with rest rooms and locker room
on the first floor. It turns out we have a better view of them (second
floor manager's offices) than they do of us as their windows are so dirty
and they are lit better. However, Bridget often get calls through the day
encouraging her to up the speed of the feed. All the conveyor belts move at
about a foot a second, but the depth of the material determines how frantic
the pace is. If it gets too deep (max of about one foot deep, two and half
feet wide) you can't even see the stuff you are suppposed to pull out and
really can't hold it back as it will just fall on the floor or, worse, into
your perforator (with the wrong material getting mixed in). The milk jugs
are the main material and largest items, so we make it easier for the people
further on. There is a pull cord along the line to stop the belts which is
what happens regularly if the feed it too fast/deep. |
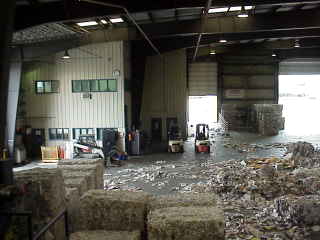 |
You can see the pull cord in this picture along the bottom
left about eight inches below the conveyor belt. The bins weren't
designed for the really long days we are working and they only empty
the bins once a day (as the compactor is backed up as well). The result
is that the milk jug and soft drink bottle bins get so full they can't
make room under the perforator. The result is that at the end of every
day we end up throwing the sorted items over the fence (about two feet
above the belt). That is a lot slower and so the feed is slowed down to
about half speed. So we are getting paid time and half to work at half speed,
but then perhaps the fixed costs of plant amortization and benefits are
already covered by the material we sorted during the first eight hours and
it works out OK. The cold drink bottle bin is only 12 feet wide (versus
18 feet for milk jug bin) and usually fills up the fastest and highest.
Here Bruce had to use his rake to push the material further into the bin so
that it didn't fall back onto the conveyor belt. |
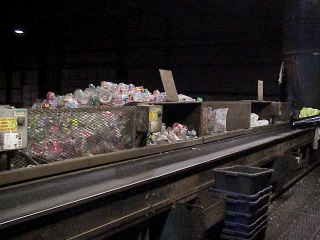 |
Here is Charles. He is an employee (and a very critical
one) who maintains all the machines, from the forklift he is driving to
the compactor/baler and sorting line. He is wearing cotton clothes as
he also welds and polyester does not do well with the sparks from welding.
I presume he takes off the polyester safety vest to weld. |
 |
This is the Matt, the manager of the recycling center.
He is a really nice guy and quite professional. I was sorry that I caught
him as he was about to speak and then didn't have a chance to get a
replacement picture. Here he is at his desk on the second floor with windows
(behind me) that overlook the center. |
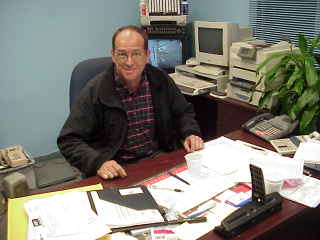 |
This is the other manager at the center. I never learned
his name (I only learn one name a day and his never came up, drats)! He
seems to work for Matt and often joined us on the line sorting. It seems
that B.F.I. always encourages it's managers to get hands on experience, which
can't help but make them better managers as they know what their people are
experiencing. However, as with many good policies, it was sometimes undermined
in very natural ways. It seemed to me that Bridget always ran the line in a much
gentler way when he was up there, not feeding it so fast, and, of course,
everyone was working their best then so it always ran smoothly (not the actual
experience we had much of the time). Oh well, what to do? |
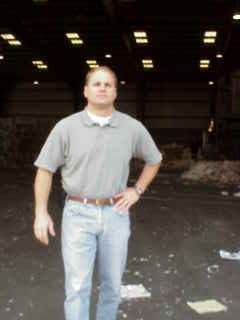 |